We’ve all been here. “This is the best they can do? Do you really need a shipping box this big? Who exactly made this decision?”
And without even seeing your offending box or what’s in it, James Malley knows the answer. A person. Mailer Box Template

“People just aren’t wired to figure out 3D space. Matching up the cubic volume of an item with the cubic volume of a box is a deceptively difficult problem to solve no matter how many times a day someone makes those decisions,” Malley says.
So, what’s the alternative? Malley, co-founder of Paccurate, has a couple of answers.
For some time now, Paccurate has been offering an application programming interface (API) to solve the problem for the cartonization of each individual shipment.
But not every company builds a specific carton for each order. So, Malley has come up with a tool, PacSimulate, that ensures the 10 or so best boxes are at each pack station. But first, let’s talk about the API.
Actually, it’s a great story, because Paccurate’s first customer was Lionel Trains. Yes, that Lionel of many people’s youth. Great place to start.
Rick Gemereth, CIO, recalls “we found inexperienced hires were trying to ‘best guess’ the right box size. We wanted to find a way to take the dimensions and weight of our trains, pack them in an optimal box, use less packaging and take the guesswork out of it.”
Actually, Gemereth’s ambitions were greater than that. He also wanted to handle a 20% increase in order traffic without hiring more people, and reduce Lionel’s small package freight costs by 10%. He got both of those plus a 100 times return on the investment in 18 months. Not bad for an API that uses data from the warehouse management system (WMS) and makes all the hard calculations itself.
Selecting the right mix of boxes at a pack station is about more than shipping orders most efficiently. It’s also about minimizing costs and reducing the number of trees needed for corrugate as well as the number of trailers that never have to be loaded.
Then there’s the matter of those pack stations that need to have a pre-set number of pre-sized boxes that are close enough to the right size for most if not all shipments.
“Gone are the days when companies can pick a set of carton sizes and run with them for 10 years. It’s not uncommon for companies to re-think their carton sizes twice a year now. Everybody’s got drift,” explains Malley.
No need for a WMS integration here. PacSimulate software runs off a spreadsheet of historical data. And it can accommodate estimates of the future mix of shipment sizes and weights.
The resulting new mix of boxes (see illustration) not only saves cardboard but can save 15% in shipping costs, Malley says. And as you already suspect, it also saves on trailer space, leading to environmental savings, too.
With much experience beyond Lionel, Malley says the environmental gains here include an average savings of 1 square foot of corrugate for each shipping carton. Depending on volumes, that can save hundreds of trees a year. He cites one company that actually required 400 fewer shipping trailers in a year. All from shipping orders in right-sized cartons.
Download this tip sheet to get your peak season preparations on track.
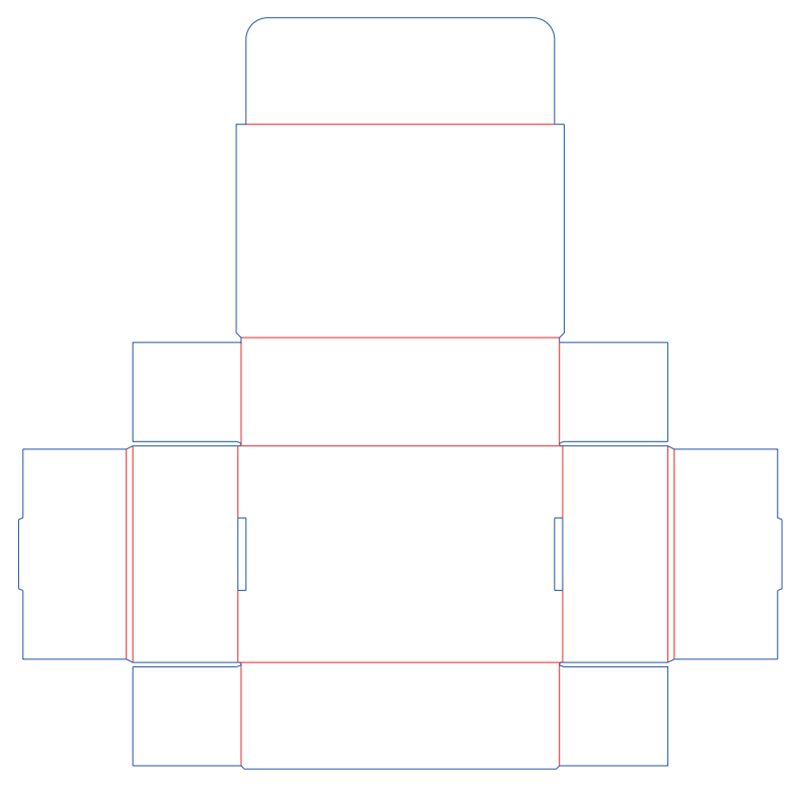
Create Packaging Tue, January 31, 2023 - 2:00 pm EST